- by yu, angie
- 2017-10-31,
- 关闭评论
质量源于设计 (QbD) —— 从溶出度测试把控产品质量
发布日期: 2017 年 10 月 31 日
质量源于设计 (QbD),意思便是当设计达到一定程度高的时候,质量自然也就随之提升,而这一概念也适用于医药行业。当药品设计可以不断突破难关,不断取得成长的时候,其带来的药品质量的提升是极为可观的,这也是药品监督管理部门推广 QbD 的主要原因。
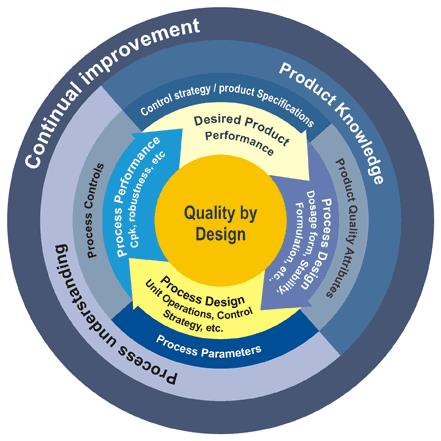
药物溶出度测试,是药品的研发和质量控制中的一个关键因素和指标。
试想一下,如果能在药品设计时,从源头 (API)、中间体和最终制剂等方面,都能整体上去掌握和把控溶出的速率,那么就将成功运用 QbD 概念,最终设计出理想的制剂。但是影响溶出速率的因素有很多,原料药 (API) 的粒径、晶型等是其主要原因,他们直接影响着 API 的生物利用度,从而左右着最终的结果。所以,测定原料 API 的溶解速率,无论是从产品设计的角度出发,还是严格去控制生产制剂的质量,都是值得去研究的方向。
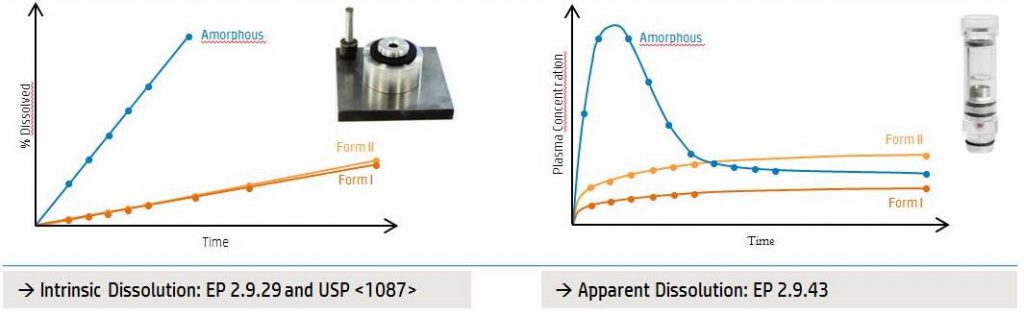
测定原料 API 溶出速率最常用的方法有固有溶出度测试法和表观溶出度法,两者之间有较大的区别。固有溶出度方法是在规定的实验条件下,测试 API 在固定表面积情况下的溶出速率。这种方法需要事先经过一系列的处理,将粉末样品经压外力制后进行测试。但是对于多晶型药物来说,施压本身有可能诱导粉末的晶型转变,因此,用此类方法所测定得到的溶出速率很有可能不是待测特定晶型下的溶出度。
另一种方法,表观溶出度,则是利用流通池法溶出度测试的原理,在保持原有 API颗粒不变的基础之上来测试样品的溶出度。利用表观溶出度方法,可以更加直观的反映出原料中不同粒径和不同晶型的溶解行为。欧洲药典中,用来测试粉末原料和颗粒中间体的溶出度便用的是这种方法。
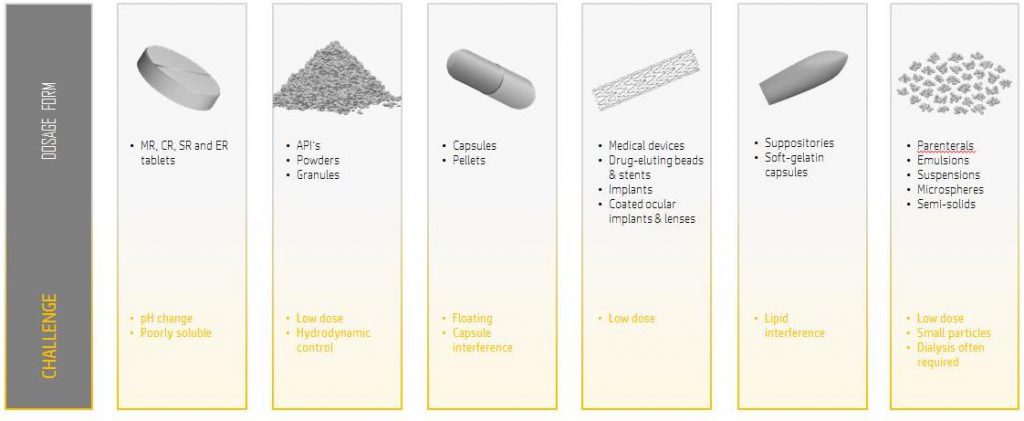
流通池法溶出度测试令人青睐的原因之一,是因为方法为不同的制剂形态设计了不同的专业流通池,也就是说,只需要用一种方法和设备,便可以完成从原料、中间体、到最终制剂一系列产品的溶出度测试。
利用流通池法,可以将产品的开发动态牢牢地掌控于开发者手中,完美呈现质量源于设计的核心理念,从而大大提升产品质量,实现药品制造的又一次跨越。
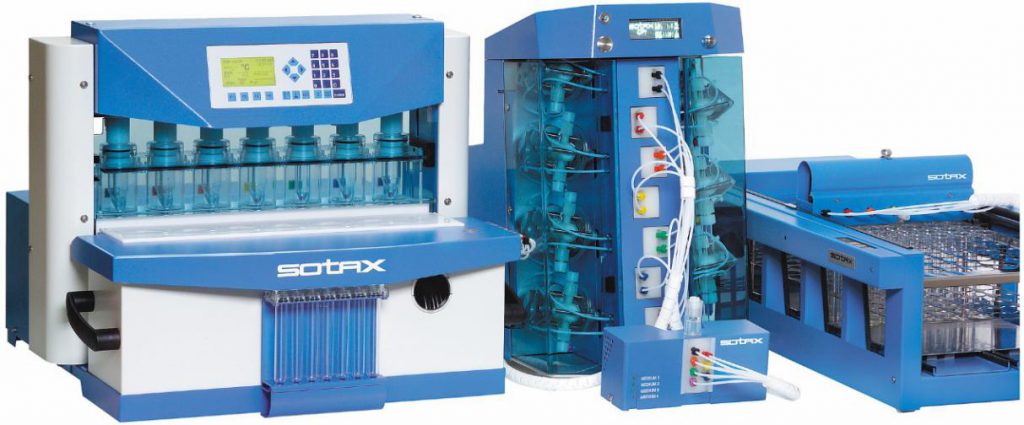